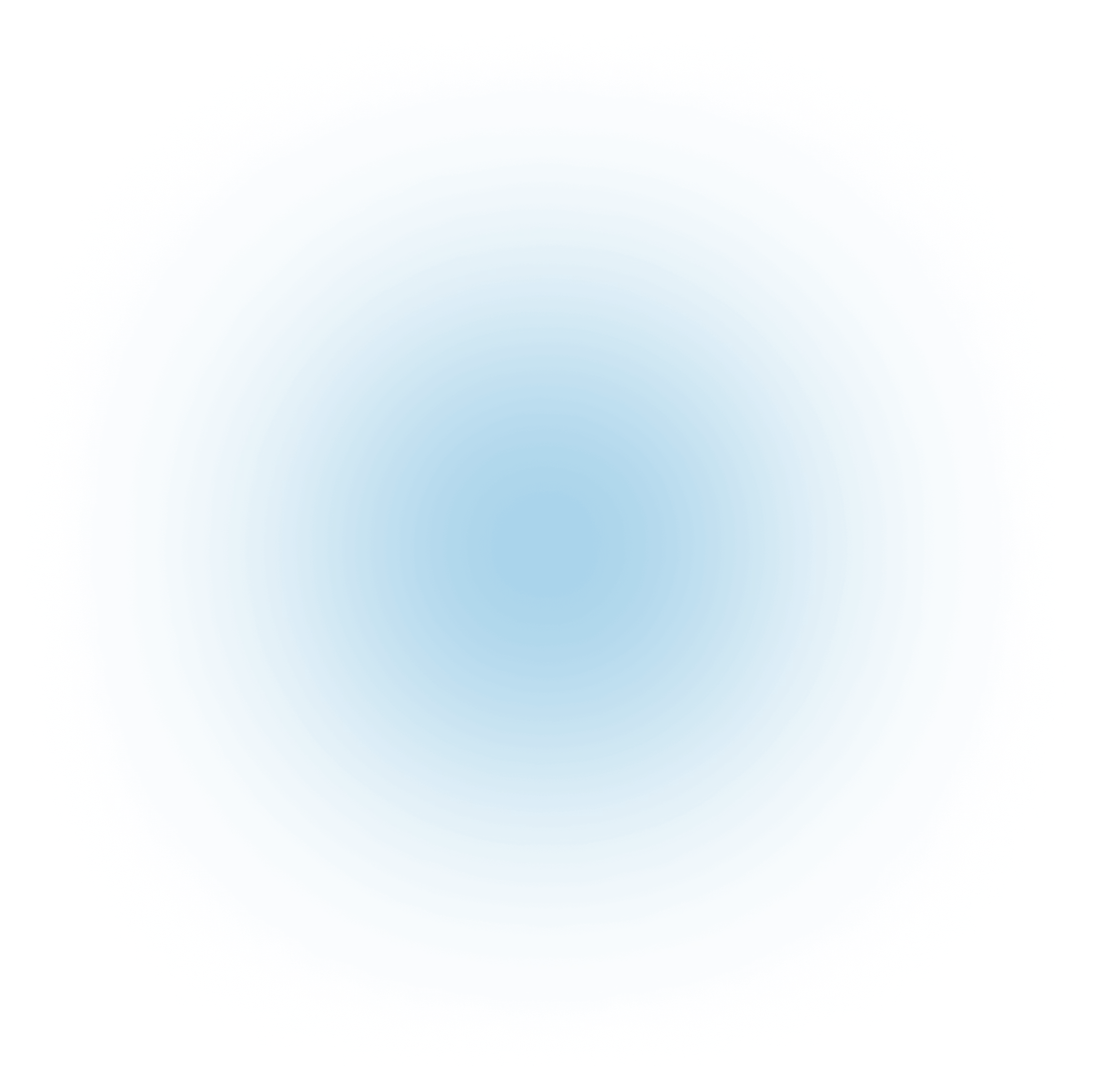
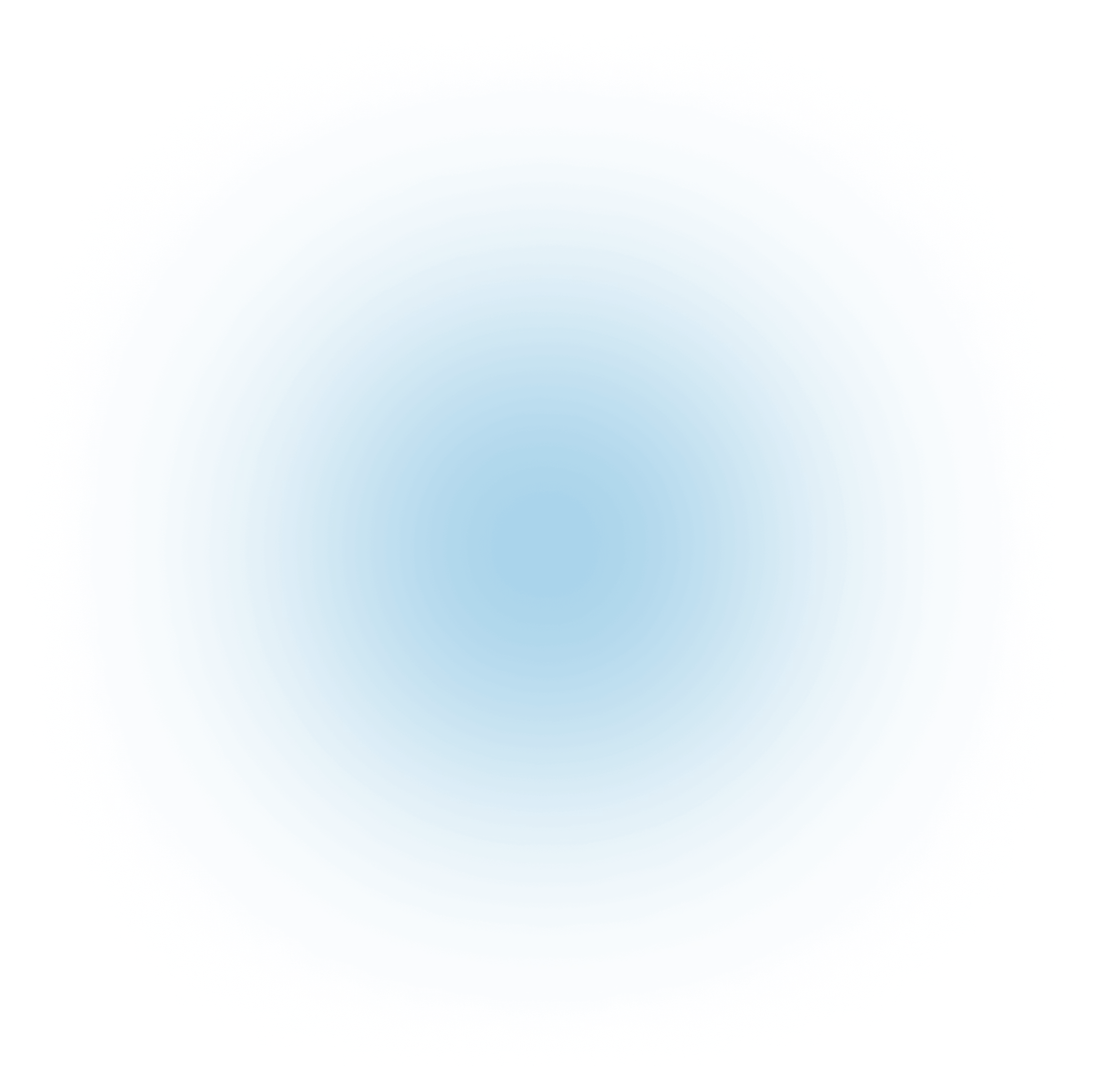
Bionics
Engineering
Our mission at Alt-Bionics isn’t just building a more accessible future for prosthetic devices, but also to build a more collaborative future for the field of bionics engineering.
When I set out on this path back in 2017, and over the years since, I realized that there weren’t (and aren’t) many good resources on how to get started in this field. A lot of the understanding that I have today was through piecemeal research and combining irrelevant projects together to create a complete and unified product.
My hope with this page is for it to be this “place to start” and to provide you with a basic understanding / overview of the field. This article is written unbiasedly and will mention our direct competitors who are all creating groundbreaking solutions.
- Ryan Saavedra, CEO & Founder
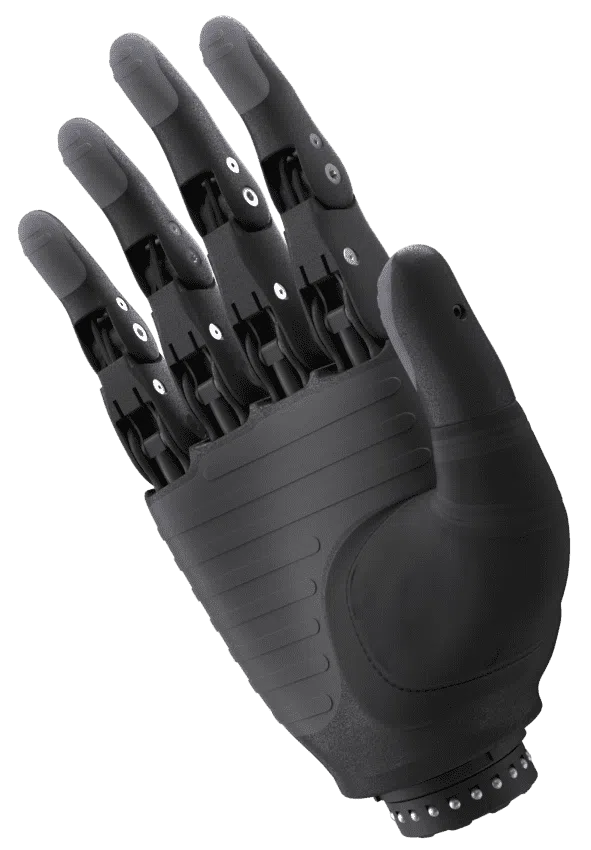
The Field of Bionics Engineering
Bionics engineering combines aspects of mechanics, electronics, and biology to create biological-inspired solutions for use in the medical and robotics field.
Some examples of devices created in this field are myoelectric bionic hands (our forte), myoelectric elbows, bionic legs, bionic eyes, bionic fingers, bionic ankles, bionic knees, and so on. The primary differentiator of the devices designed in this field, and as the word “bionic” denotes, is that the technology / devices created are typically electromechanical in nature. This means that in addition to being able to move mechanically, their mechanical components are powered using a power source (battery) and some type of accompanying circuitry to manage the control of the components.
Please note that I said they are “typically electromechanical in nature”. However, in addition to the above listed electromechanical devices, within the field of bionics engineering there are also devices that are not electromechanical. These devices are called body powered devices or prostheses. These devices’ movements are dependent on a system of cables and harnesses (as well as other manual controls on the devices) to control the limb in a simplistic, yet effective manner. Although functionality of these types of devices are limited, they are often used more than electromechanical ones.
“More often? But why?” you might ask; The primary reasons that these less advanced devices are used more are quite simply ease-of-use and cost. This is however, a disputed claim, and I urge you to perform your own research to come to your own conclusion around this matter.
Helpful Links
College Degrees & Bionics vs Prosthetics
“Do I need a biomedical engineering degree?”
The most common misunderstanding about this field of research is that you need to study Biomedical Engineering to build bionic limbs. I have received a many number of emails from biomedical engineering students citing that this field is exactly why they got into BME. It is difficult for me to tell them that the work we do is not as dependent on BME studies as they may believe.
Though it doesn’t hurt to study this, the truth is that the work building these bionic devices is much more reliant on Mechanical Engineering and Electrical Engineering. So please don’t be deterred by thinking that you need a biomedical engineering degree! Mechanical and electrical engineering are just as important! The only aspects of biomedical engineering that I personally needed to understand to build a full functioning bionic hand that an amputee could control was a little bit of physiology (action potential). I will go over this topic in more detail further down this page as the sections are built out more.
“Bionics Vs. Prosthetics!?”
The second most common misunderstanding about this field is that it is called “Prosthetics”. While this word does accurately denote and describe an artificial body part, the FIELD of prosthetics is something entirely different. In fact if you type in “how to get into the field of prosthetics”, the first Google results direct you to a degree in orthotics and prosthetics.
A degree in Orthotics and Prosthetics are for those interested in becoming prosthetists and orthotists. Prosthetists and orthotists design and fabricate medical supportive devices and measure and fit patients for them. They are typically responsible for crafting the prosthetic socket (see below), creating highly customized prosthetic solutions, continued patient care, and repairs or tuning of bionic devices. In rare instances, prosthetists may include basic circuitry or wiring into their custom devices, but they do not create bionic devices.
I only mention this differentiation because while most people are interested in bionics engineering, some people do in fact want to be prosthetists! I admire both fields for their collaborative work towards building a more accessible future. The question is, which do you like more?
Bionic Hands vs. Prosthetic Sockets
In this section, we delve into the practical application of the disciplines discussed earlier, highlighting the critical differences and connections between bionic hands and prosthetic sockets.
Bionic Hands:
Bionic hand companies like Alt-Bionics, Psyonic, and Aether Biomedical all create bionic (myoelectric) hands that are standalone devices. If you were to purchase a bionic hand from a manufacturer like us, you would only have a bionic hand with no way to use it.
Prosthetic Sockets:
Prosthetic sockets provide the interface between a bionic hand and the user’s body. The socket is custom-fitted to the user’s limb and is usually made from soft and flexible materials to ensure a comfortable fit. They evenly distribute the weight of the prosthetic device and enable the user to move the device with relative ease.
Prosthetic sockets are designed and built by certified prosthetic & orthotic clinicians who are typically part of prosthetic clinics like Hanger or Arm Dynamics. These clinics and clinicians do not build hands. Their primary responsibility is to create sockets, provide continued patient care, and help the amputee select the prosthetic device that will be best for them.
Building Your Own Bionic Hand
Building bionic hands is a multidisciplinary journey that merges the intricacies of mechanical and electrical engineering with a touch of biology. At its core, constructing a bionic hand involves designing and assembling an electromechanical device that mimics the functionality and appearance of a natural hand.
Getting involved in this work is honestly just a matter of researching what interests you the most and finding some good, trustworthy (peer reviewed or generally accepted) articles on whatever you find interesting
However, below is often my advice on anyone looking to build their own or learn a little more.
Let’s start with the brain. Every time you want to move any muscle in your body, your brain first needs to generate a signal (an electrochemical signal to be precise) to be sent out. This signal has a voltage associated with it (roughly 40mV at its peak). That signal is then propagated throughout your central nervous system (CNS) to reach the appropriate muscle. Once it reaches the appropriate muscle, this electrical signal excites your muscles and forces them to tighten (or flex)
On to the electromyography circuit (EMG). The EMG picks up these muscle signals (again, around 40mV) and amplifies and filters them into something much larger and cleaner (the microcontroller, or MCU, likes larger, cleaner signals — 0-5V). These signals are best gathered from muscles closest to the surface of the skin (also called Superficial muscles).
Finally the MCU and the Hand. The MCU is coded to recognize the amplified signals and can then use them however the programmer sees fit. In our case, we use them to move the hand by either proportionally mapping the voltage to how much the fingers flex, or by preprogramming grips. This process goes into much more code based detail, but that is essentially the idea.
Below you will find some resources that helped me create this. I hope this helps.
- BrunelHand 2.0 Assembly: https://www.thingiverse.com/thing:3000641
- Myoware Muscle Sensor: http://www.advancertechnologies.com/p/myoware.html
- PQ12-R Actuators: https://www.actuonix.com/Actuonix-PQ12-R-micro-linear-servos-for-RC-p/pq12-r.htm
- ArduinoKit: https://www.amazon.com/gp/product/B009UKZV0A?pf_rd_r=5XTFNBBMXY59EV453DCH&pf_rd_p=edaba0ee-c2fe-4124-9f5d-b31d6b1bfbee
- SyntheticSkin:https://www.amazon.com/gp/product/B00IZNEPF0/ref=ppx_yo_dt_b_search_asin_title?ie=UTF8&psc=1
- Sensors: These are crucial for detecting user intent and providing feedback.
- Force sensors
- EMG sensors
- Accelerometers
- Actuators: These small motors are responsible for moving the prosthetic fingers and thumb, mimicking natural hand movements.
- Rotary
- Linear
- Pneumatic
- Control Systems: Microcontrollers and software algorithms process sensor data and control the actuators, ensuring precise and smooth operation.
- Arduino
- STM32
- NRF
- Power Supply: A reliable power source, typically a rechargeable battery, is essential to keep the bionic hand functioning throughout the day.
- Lithium-ion
- Nickel-metal hydride (NiMH)
- Lead-acid
- Materials: Durable and lightweight materials like medical-grade rubber, silicone, and high-strength plastics are used to construct the hand, ensuring comfort and longevity.
Creating a bionic hand (from scratch) involves several intricate steps, each requiring precision and expertise:
- Design and Prototyping: The process begins with designing the hand using CAD software. Prototypes are then created using 3D printing to test form and function. Hundreds of prototypes may be necessary to achieve a final design. (Please be mindful of waste and try to really focus on making it perfect every prototype iteration).
- Component Integration: Sensors, actuators, and control systems are integrated into the prototype. This step involves a lot of testing and iteration to ensure all components work seamlessly together.
- Software Development: Custom software is developed to control the hand, process sensor inputs, and provide feedback. This includes writing algorithms for motion control and user interface development.
- Testing and Calibration: The hand is rigorously tested to ensure it performs well under various conditions. Calibration is done to fine-tune the sensors and actuators for optimal performance.
- Final Assembly: Once all components are tested and calibrated, the final assembly takes place. The hand is then packaged and prepared for delivery to users.
Building a bionic hand comes with its own set of challenges and considerations:
- Precision and Accuracy: Ensuring that the hand movements are precise and accurate to mimic natural movements is a significant challenge.
- Durability: The materials and components must withstand daily wear and tear while remaining lightweight and comfortable for the user.
- Power Management: Balancing power consumption with performance is crucial to ensure the hand can be used throughout the day without frequent recharging.
- User Adaptability: The hand must be adaptable to different users’ needs and preferences, requiring customization options and adjustable settings.
- Cost: Keeping the production cost low while maintaining high-quality standards is essential to make bionic hands accessible to a wider audience.
The field of bionics engineering is rapidly evolving, with new technologies and innovations on the horizon:
- Advanced Sensors: Future bionic hands will feature even more advanced sensors, capable of providing more detailed feedback and improving user control.
- Artificial Intelligence: AI and machine learning algorithms will play a significant role in enhancing the functionality and adaptability of bionic hands, making them smarter and more intuitive.
- Improved Materials: Research into new materials will lead to lighter, stronger, and more comfortable prosthetic devices.
- Integration with Neural Interfaces: Advances in neural interface technology will allow for more seamless integration between the user’s nervous system and the bionic hand, enabling more natural and intuitive control.
- Wider Accessibility: As technology advances and production costs decrease, bionic hands will become more accessible to a larger population, improving the quality of life for many individuals worldwide.